SAP MRP機能の活用ポイントと限界&解決策とは?(vol.68)
- 公開日:
- 最終更新日:
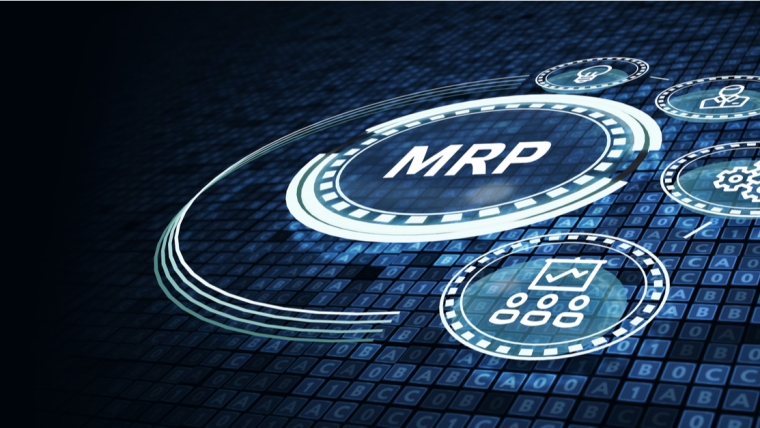
製造業のSAPユーザでPP(生産計画/管理)モジュール導入済み企業の多くが、半製品や中間品の製造計画や、原材料や部品の購買計画を立案するために、MRP(Manufacturing Resource Planning)機能を利用しているかと思います。
MRPの歴史は古く、1960年代に米国で考案され、1970年代から80年代にかけて、MRPを組み込んだソフトウェア製品が相次ぎ登場することで急速に普及しました。日本にMRPの考え方が持ちこまれた当初は、日本のかんばん方式と比較し、”アメリカ式かんばんシステム”とも言われていました。
業種や生産形態(見込生産/受注組立生産/受注生産/個別受注生産 等)、生産方式(ジョブショップ型、ライン型、セル型 等)によりMRPの有効性は異なりますが、本ブログでは、MRPを上手に活用するためのポイントと、MRP機能単独では解決できない課題=MRP機能の限界&その解決策を解説します。
*SAP S/4HANAで利用可能なMRP機能「MRP Live」の特徴や「Classic MRP」との差異、「MRP Live」のパラメータ値や並列処理設定方法などについては、こちらのブログ記事をご覧ください。
目次
SAP MRP機能を活用するためのポイント(不可欠な要素)とは?
MRPは、必要なモノ(品目)を、必要なとき(納期)に、必要なだけ(数量)、製造したり購買したりするための手法です。MRPが普及する以前よりあった発注点方式やダブルビン方式と比較し、ジャストインタイムにモノを製造・購買するのに適した手法です。MRPを正しく運用することで、原材料や半製品の調達・製造をコンピューターで過不足なく自動的に管理できるようになり、在庫削減や生産性の向上を効果として期待できます。一方、発注点方式やダブルビン方式 等の物理的な管理方法と比較して、効果的に運用することが難しい仕組みです。
皆さんご存じかとは思いますが、まずはMRPのロジックを解説します。
独立需要として、生産計画または受注情報を登録することより開始し、以下の手順①~⑤を上位品目よりレベルバイレベルで最下位品目まで繰り返すことで、全ての従属需要品目の計画手配を作成します。
手順 | 各手順の説明 |
① 総所要量計算 | 上位品目より要求される数量(例えば、製品X,Y,Zで使用される子品目aについては製品X,Y,Zからの要求数量)を、タイムバケット別にまとめ総所要量を計算します |
② 正味所要量計算 | 計算された総所要量より、出庫予定/入庫予定/在庫数量/安全在庫数量を加味し、正味所要量を計算します |
③ ロットまとめ | 計算された正味所要量より、ロットまとめ方式やロットサイズに基づき、手配に適した数量にまとめます |
④ リードタイム計算 | 手配納期より、マスタに設定されているリードタイムを差し引き、着手日を計算し計画手配を作成します |
⑤ 所要量展開 | 作成された計画手配より、BOMを参照し下位品目の所要量を計算します |
では、MRPをうまく活用するために不可欠な要素は何でしょうか?
上述のロジック説明内にも登場する言葉ですが、以下の3つの精度向上が必要です。これらの精度が低いと、MRPで計算される従属需要品目の計画精度も低く、MRP導入により返って生産現場の混乱を招いてしまいます。
- 生産計画の精度
生産計画は、MRPを実行する大元の数値となります。刻々と変わる販売状況や製品在庫状況、顧客からの内示や受注、大口顧客からの引き合い情報を生産計画に素早く反映させ、必要なもの、優先度の高いものを過不足なく作れるよう、生産計画の確定期間および生産計画の立案サイクルはなるべく短く運用し、生産計画精度を高めていくことが必要です。
また、原材料・部品~半製品~製品の製造の負荷を平準化させるために、生産計画レベルより負荷の平準化を試みることも重要です。 - マスタ(BOM 等)の精度
MRPは、BOM 等のマスタ情報を参照し、従属需要品目の計画手配を作成します。その為、品目マスタのリードタイムやロットサイズ、BOMの構成品目や員数、不良率が正しくないと、従属需要品目の計画手配は正しく作成されません。
マスタは一度設定すれば終わりではなく、実際の製造状況に合わせて、リードタイムやロットサイズ、不良率 等の見直しは必要です。また、設計変更時は、設計変更前の構成品目で手配データが作成されないよう、正確に速やかにマスタに反映させる必要があります。 - 在庫の精度
3つの精度のうち、最も大切なのは在庫精度です。筆者がシステム導入したお客さまで、在庫精度が悪いがために、MRPが自動で作成する従属需要品目の計画手配を、人手で調整した苦い経験があります。在庫精度は、98%以上ないと、MRPは効果的に運用できないと言われていますので、在庫精度が上がるまでは、MRPの本格運用は避けた方が良いでしょう。在庫精度を上げるためには、入出庫情報の入力をリアルに行うよう現場教育を行ったり、定期棚卸以外に循環棚卸を取り入れる等の在庫精度向上施策を徹底的に行ったりする必要があります。
SAP MRP機能の限界と解決策①:生産能力を加味した計画立案
MRP機能の限界の1つ目は、無限負荷山積の生産計画である点です。すなわち、生産設備や現場作業者 等のリソースの制約条件は加味しない計画である点です。ジョブショップ型の加工企業や、ボトルネック設備や工程を持つ企業 等、資材制約よりも能力制約がある工場で、この問題に直面します。
システム面での解決策としては、負荷の山積み、山崩し機能を保有したスケジューラソフトとMRPとの併用です。スケジューラソフトとしては、SAPのPPDS(Production Planning and Detailed Scheduling)や国産のAsprova / Flexsche 等が、代表的なソフトになります。
いずれのソフトも、生産設備や現場作業者の能力制約を予めマスタとして設定しておくことで、負荷が能力を超える場合、負荷の山崩しをシミュレーションできる機能を保有しています。
一方、スケジューラソフト導入のメリットを享受するためには、MRP以上に能力や負荷を計算するためのマスタ精度向上が必要となります。
SAP MRP機能の限界と解決策②:直近の需給変動を加味した計画立案
MRP機能の限界の2つ目は、需要変動が発生した際、MRPは手配日付・数量の再計算を行ってくれますが、再計算の対象が計画手配である点です。すなわち、計画手配から製造指図・購買依頼へ変換した確定手配は、再計算の対象外となります。
確定手配に対してMRPは変更を促す警告を発しますが、警告の量が多い場合、警告を参照しながらの対応は現実的ではありません。また、MRPで警告を発するのは、1レベル下位下層の品目までで、多段レベルで下位品目に展開し、警告を行ってくれるわけではありません。例えば、受注納期に変更があった場合、最終製品の製造指図の納期までは警告を発しますが、半製品の製造指図や原材料の購買発注の納期に対する警告は発しません。
生産準備に工数を要する等で確定手配期間を比較的長くとる必要がある企業で、顧客からの需要変動が多く発生する、または原材料や製造が計画通り進まないケースで、この問題に直面します。業種的には機械製造業 等で、生産形態として受注組立(ATO)、受注仕様組立(CTO)、受注加工組立(BTO)の製造業で、この問題をよく耳にします。
システム面での解決策としては、確定手配も含めた需給バランスをシュミレーションできるソフトの利用が考えられます。前述のスケジューラソフトでも対応可能なものもありますが、当該用途での利用を考えると、機能的にToo muchで使い易くもないため、当該用途専用ソフトの利用がお勧めです。
SAP MRP機能の活用ポイントと限界&解決策 まとめ
本ブログでは、SAP MRP機能の概要をご説明のうえ、MRP機能を上手に活用するために不可欠な要素や、MRP機能単独では解決できない課題=MRP機能の限界とその解決策を解説しました。
電通総研は、多くの製造業の基幹システム導入を支援する中で、「MRP機能の限界②:直近の需給変動を加味した計画立案」を解決するノウハウを保有するに至りました。もし、「需給バランスをシュミレーションすることで、直近の需給変動を加味した計画立案をしたい」といったご要望がございましたら、是非、電通総研までお声掛けください。
※本記事は、2022年3月31日時点の情報を基に作成しています。製品/サービスに関する詳しいお問い合わせは、電通総研のWebサイトからお問い合わせください。
https://erp.dentsusoken.com/inquiry/